America's Roller Coaster Ride to Peak Manufacturing Performance
- admin987020
- Sep 6, 2018
- 8 min read

As the train lurches upward to this wooden mountain’s 205-foot apex, the methodical clacking of the ratcheting teeth underneath count down to impending exhilaration. On the left, the immaculate azure sky plunges into the dark surface of Lake Erie. In a few seconds, I’ll drop 90 deg at a rate of 74 mph. The 200-ft. vertical descent on this massive roller coaster called Steel Vengeance, Cedar Point’s newest thrill ride, will take less than 2 seconds. Spanning the total length of track—more than a mile at 5,740 feet—takes 150 seconds, much of it climbing this first hill. I, like everyone without a Fast Pass, waited two hours in line for this. For now I’m enjoying the view of "America’s Roller Coast," and the anticipation of what’s about to come.
Steel Vengeance opened this May in the Sandusky, Ohio amusement park. The world’s first "hyper-hybrid" coaster was built over the last two years upon the wooden skeleton of Mean Streak, a rickety ordeal that bruised and battered riders for a quarter-century.
Built by Rocky Mountain Construction, which specializes in hybrids, this—their magnum opus—lords over a peninsula full of colossal coasters. At one time, nearly each had their turn as king of the amusement world, from the first hyper coaster, the Magnum XL-200, to Millennium Force, a 300-foot "giga" coaster 11 years later. Neither bigger nor faster than either, Steel Vengeance nevertheless reigns supreme because it modernizes the old way with the latest in engineering and technology without wasting a perfectly good, if not a bit old-fashioned, foundation.
It’s in an industry that’s literally all fun and games, but this modernized marvel epitomizes what should happen in the traditional manufacturing sector. Legacy systems and old-timers don’t need to be cleared away like overgrown brush to make way for smart machines and tech-savvy twentysomethings. Why waste all that perfectly good experience and character? At the same time, people crave a faster and better, smoother and increasingly adventurous experience. The competition here reflects the current global dynamic as well: The no-frills, only-thrills park is America’s preeminent engineering wonderland, and was named world’s best amusement park by leading trade mag Amusement Today for 16 years, before being dethroned by the more garish German doppelganger Europa-Park (the title-holder since 2014). America has a drive to be the best, and keeping what works and tweaking what doesn’t may be the best way to get there.
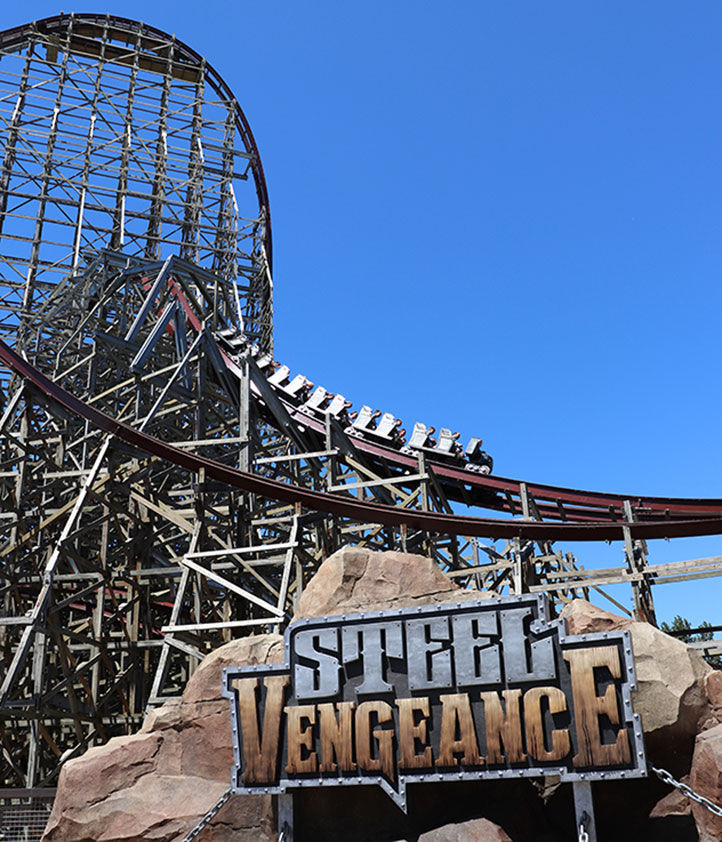
Thrill ‘Em with Kindness
Mean Streak reached a top speed of 65 mph and had a 22% shorter first drop—with a relatively mild vertical slope of 52 degrees. One man, "Mean Streak Henry" Sievers, rode it 16,000 times, though I, like many, rode it mostly out of some unwritten masochistic obligation.
After cresting the first hill and completing the Steel Vengeance experience, fraught with furiously frantic twists and turns (four inversions and a world-record holding 27 seconds of airtime), I would feel obliged to wait even four hours to go another round.
"Steel vengeance is the one people are going to want to start on and finish on," says Tim Baldwin, editor of RollerCoaster!, a magazine for members of the group American Coaster Enthusiasts. He estimates he’s notched more than 1,000 different rides in his life.
After his June trip to Sandusky, Ohio, Steel Vengeance instantly became his favorite ride in one of his favorite parks. He has been to Europa-Park and does love that one, too.
"It’s just all over the place," Baldwin says of Steel Vengeance. "I love the direction changes. But it’s done comfortably and is very fluid. It’s like watching ballet while riding a bucking bronco."
Personally, I agree with the bucking aspect of it. But instead of a run of the mill bucking bronco, it’s like trying to break a Pegasus on PCP. And even while bulleting through abrupt wooden tunnels and then turned upside down, I felt completely comfortable going hands up through the entire ride, as my legs were locked down by cushiony braces, along with a lap bar. I felt safe and secure the whole time, free to absorb the gratuitous airtime.
"Rides are bigger, wilder, faster, but I think they’re safer than they’ve ever been, just because technology and computers can just do more," Baldwin says.
That’s because of the designers, engineers and builders who made Steel Vengeance—who in Baldwin and other coaster enthusiasts’ adrenaline-packed universe are as highly regarded as superstar athletes or award-winning artists. Teams’ and musicians’ quality will inevitably decline; Steel Vengeance may drop precipitously, but uses that momentum to get right back up.
Lessons for the Factory
Besides admiring the daredevil geniuses who sculpted this monument to unadulterated joy, why not steal from them? There’s much manufacturing wisdom snuck into the maze of beams and rails.
First, there’s the matter of design time. Rocky Mountain’s engineering experts, much like the noble hermit crab, know a good shell when they see it. And have since they started building hybrid coasters nearly a decade ago. Instead of starting from nothing, they simply built off of what exists to make it better. Even the most brilliant automotive minds of today stands on the shoulders of a century’s worth of innovative giants, from Henry Ford to Elon Musk.
It’s also incredibly economical. Tearing down more than a mile of track and removing tons and tons wooden support beams would be incredibly expensive. No new construction could be completed until it was all clear, meaning less guests through the turnstiles to buy marked up soft drinks and Dippin’ Dots. Similarly, any manufacturer wants to get new production lines up and running as quickly as possible. As John Kawola, Ultimaker’s North American president, recently told me, if you’re a month late to launch, you don’t make that revenue back.
Traditional wooden coasters require more maintenance and the entire length of the track has to be checked daily. In regards to manufacturing equipment, the total cost of ownership (TCO) represents a fraction of overall costs, while much is eaten up by maintenance. Upgrading may seem more expensive, but money can be saved in the long run by fewer stoppages that cost man hours and impede production.
Rocky Mountain’s patented IBox track eliminates the need for wood stacks, allowing for the previously impossible inversions. This is the same as adding IoT sensors to teach an old CNC machine new tricks, or installing a collaborative robot on the line to assist workers for faster assembly times.

Safety First
"A lot of people don’t realize the technology used in amusement industry is the same automation tech used in the factory," says Linda Freeman, Rockwell Automation’s business development manager for the entertainment industry. "Automotive plants want people to work collaboratively and not put guards up. Those are engineering concepts from the theme park business."
There are safety gates, of course, which only open when the train car is stopped, because theme parks do have the tendency to bring out the dumb in people. The point is, though, that people interact with this powerful machinery, and only strap in because they trust that they won’t fall out during a barrel roll. And that the brakes will activate when they need to.
To safely ensure that happens, the ride relies on a safety programmable logic controller, just like a robot or virtually any automated piece of machinery.
"Where the PLCs really do a lot of work is when you’re coming into a brake run," says Brian Ondrey, of Steel Vengeance’s motion control integrator Irvine-Ondrey. "It does speed calculations, and through that calculating is how to slow the ride down, and how long to activate the braking. You have to plan for unknowns in the system, like different speeds. You’re never going to come into the break at the same speed."
Irvine-Ondrey picked Rockwell’s GuardLogix 5570 Controller, which not only opens and closes the braking system, but monitors proximity switches on the track and e-stops. They work by constantly hailing a signal to ensure each input has an open line of communication. When interrupted, the system goes directly to safe mode, which would mean locking the train in place. The alternative could be that the brakes don’t activate and one train car smashes into another.
Two Steel Vengeance cars were involved in minor bumping incident on opening day in May, but Ondrey asserts that it had nothing to do with the PLC, though couldn’t comment further.
What has everything to do with GuardLogix controller is ease of integration.
"Back in the day, we had to run wires for everything from the main cabinet," Ondrey says. "Now all we have is Ethernet and main power going to each section of the ride."
Remote I/O switches act a waystation for the various inputs, such as proximity switches.
What separates safety PLCs from normal ones is the redundancy. The command codes are stored in protective memory and cannot change.
Since being launched in 2005, the GuardLogix line has become the premier safety PLC for the amusement industry, says Brad Prosak, a Rockwell product manager for safety controllers.
The greatest advantage of having a safety PLC like the GuardLogix is the internal redundant architecture perpetually checking that the hardware will run as expected all on one product.
"Before GuardLogix, they were building safe rides, but what they were doing to achieve that is to build two of everything, so there was no single point of failure," Prosak says. "Two control systems checking the same sensors, and controlling the same output to deenergize if the situation ever arose."
This would make the initial validation test extremely time intensive, as two engineers would have to independently code the various programming, then cross-check, or peer review, each other’s work to make sure they match up.
The automotive industry uses the GuardLogix to control the skids that carry chassis around the factory floor. If they had to cross-check, Prosak says it could take months.

Newly released versions of the 5000-series have faster processing power and allow for the choice of lower levels of scaling, a compact footprint and simpler architecture, Prosak says. Sometimes the automation is simple and you may have to run a light curtain for a fenced-in industrial robot application, or it can be a crowded work cell with cobots and humans working side-by-side.
And Freeman says that getting these safety controls right on a roller coaster, one rife with death-defying turns and hordes of hyper children, proves that they will work in manufacturing. In fact, Rockwell sees their products engineered for amusement become actual muses for future plant innovations.
"We look toward the entertainment industry as a technology indicator for where manufacturing will be going in the future," says Freeman, pointing directly to the advances in dark rides, ones with carts inside a building that rely on audio and video to stimulate the senses. "You need very accurate position and time control. If you don’t have that, the guest will get sick because the body can tell something is out of sorts."
Final Thoughts
Leaving the park that night, with my body perfectly in sorts, I thought about all the extremes I experienced throughout the day. Like when I was shot up a 420-ft. hill at 120 mph in 4 seconds on Top Thrill Dragster. This strata-coaster launches the 15,000-lb car via a hydraulic system that generates 10,000 HP. It repeats that every few minutes for most of the day, though high winds and other factors can induce temporary stoppages. It’s amazing that it does this at such a height, speed and acceleration so smoothly and safely.
It’s a heart-pounding, but fleeting, ride. A good-while-it-lasts kind of thing. Weeks later, Steel Vengeance is still with me, mostly due to the shame I carry from giggling so much as grown man. I will also still always remember Mean Streak, but mostly because it was Cedar Point’s equivalent to a prostate exam: tolerated out of utilitarian necessity.
I’ve found that manufacturing operates the same way. If you go all-new and flashy, you’ll have unsustainable success. If you stick with the old, you’ll get the job done but it will be full of pain points. If you merge the best of both worlds, whether it’s with your workforce or equipment, you may get more something exponentially better than either part. Sometimes, you may even get Pegasus.
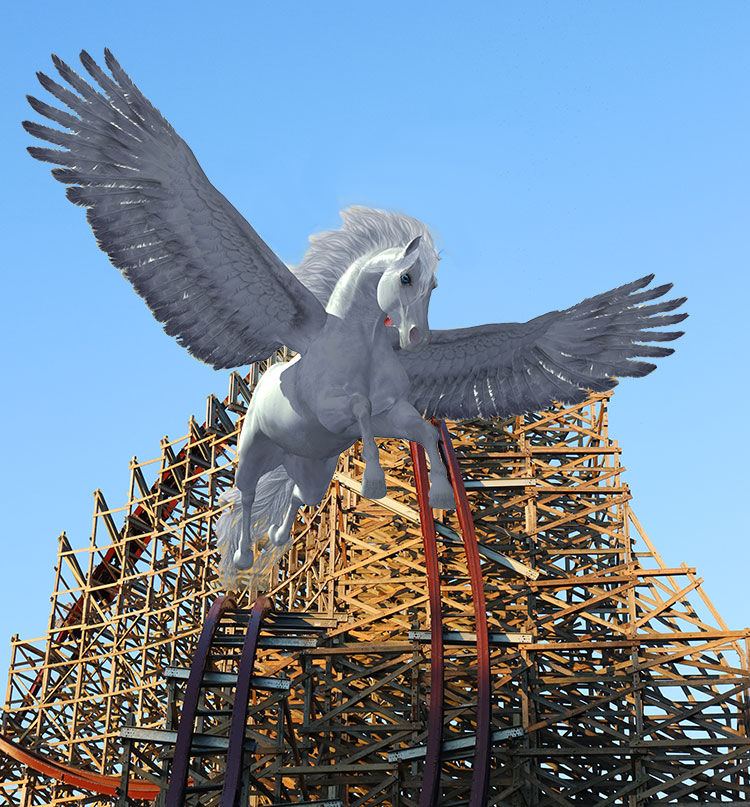
Comentários